1. Learn about vacuum bags
a. What is a vacuum, why should it be vacuumed?
Vacuum or vacuum packaging is a packaging method that completely removes the air in a package before sealing it. The purpose of this form of packaging is usually to remove oxygen from the container to extend the shelf life of the food, preventing them from spoiling.
Reducing the amount of oxygen in the environment will limit the growth of bacteria or fungi, while also preventing the evaporation of volatile components. Vacuum bags are ideal for long-term storage of dry foods like cereals, seasonings.
On a shorter-term basis, vacuum packaging can also preserve fresh foods. In this case, vacuum sealing is often accompanied by freezing to increase storage capacity.
In addition, the vacuum is also used to reduce the weight and size of the product after packaging. Pillowcases or mattress rolls are good examples for this packaging purpose. If not vacuum sealed, they not only become extremely space-consuming to store, but also make it difficult for consumers to buy and ship them to home. It can be seen that although vacuum packaging is expensive, it is a necessary step to increase the competitiveness of brands in this case.
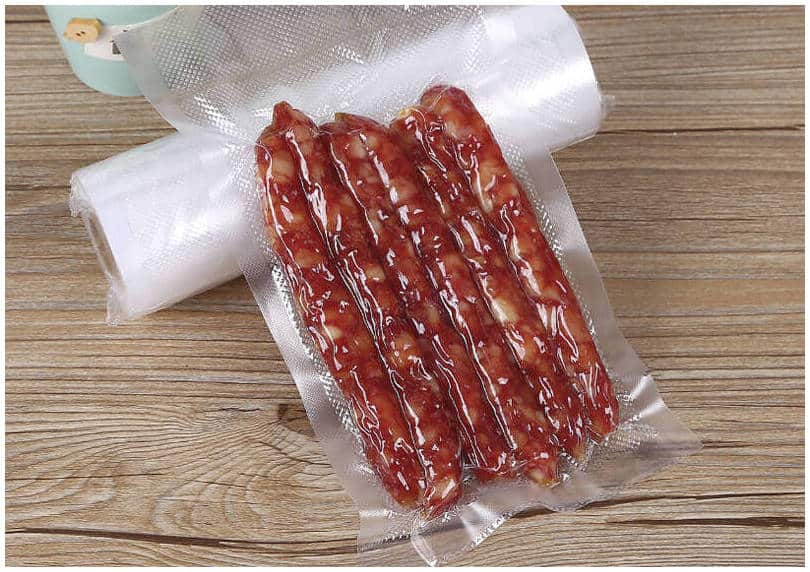
b. What are the special features of vacuum bags, what material are they made of?
Depending on the purpose of packaging, we can use single-layer plastic bags or laminated film packaging (multi-layer) to vacuum.
In theory, all types of plastic bags can be vacuumed, as long as they are thick enough to not tear under the strong suction of the vacuum. After the air is sucked out and sealed, the packaging must remain intact so that air does not re-enter the interior. For the purpose of vacuuming for family activities, most types of thick enough plastic bags can meet well.
However, in industrial production, the story is completely different. Vacuum bags for frozen foods require the ability to withstand low temperatures for a long time without drying out, a phenomenon that common plastic materials such as LDPE, HDPE or PP all face.
As for the purpose of packaging to minimize the volume and volume of packages such as pillowcases, comforters, mattresses, etc., The packaging used needs to be soft and flexible but still has to be strong enough to withstand extreme suction, compressing the product inside to the smallest possible size. High-thickness Low-density Polyethylene (LDPE) bags can meet these packaging requirements. When the vacuum cleaner sucks the air out of the package, it creates wrinkles and shrinks on the package. With stiffer materials such as Polypropylene (PP) or High-density Polyethylene (HDPE), these creases can form tearing folds that lead to packaging failure. Vacuum LDPE bags can also be added to the material tank when being produced, adding a toughness additive to the material tank, which improves packaging performance significantly.
Returning to the vacuum-sealed plastic bag for frozen food, manufacturers need to find a material that can withstand strong suction to completely remove the air inside, and can withstand freezing temperatures for a long time. There are many engineering plastics that can meet this requirement, but they have problems with heat sealing. And most importantly, they have not been proven to be safe and approved for food storage according to the standards issued in many countries. Using such packaging would be very unsafe, and the product contained inside would almost no longer have a chance to be exported.
And the main solution is a type of laminated film packaging made up of many layers of materials combined to create outstanding properties, with the innermost layer in direct contact with the product being food safe materials (LDPE). and outer layers are engineering plastics with outstanding properties.
There are many types of vacuum bags with different compositions such as PET/PE, PA/PE, PE/PA/EVOH, OPET/PP, OPA/PP, etc. There are also bags due to special requirements that are composed of 5, even 7 different layers of film. The selection of the right type of vacuum bag will be based on the needs and responsiveness of each type of material that makes them up. For example, bags made of PA/PE are safe to boil at 100°C, but cannot be sterilized at 121°C, but PA/PP or PET/PP bags can. This is because the melting point of PE is only 120°C and PP is up to 165°C.
There is one thing in common among all vacuum bags currently on the market, is that they can all be considered freezer safe, because this is the core purpose of this type of packaging.
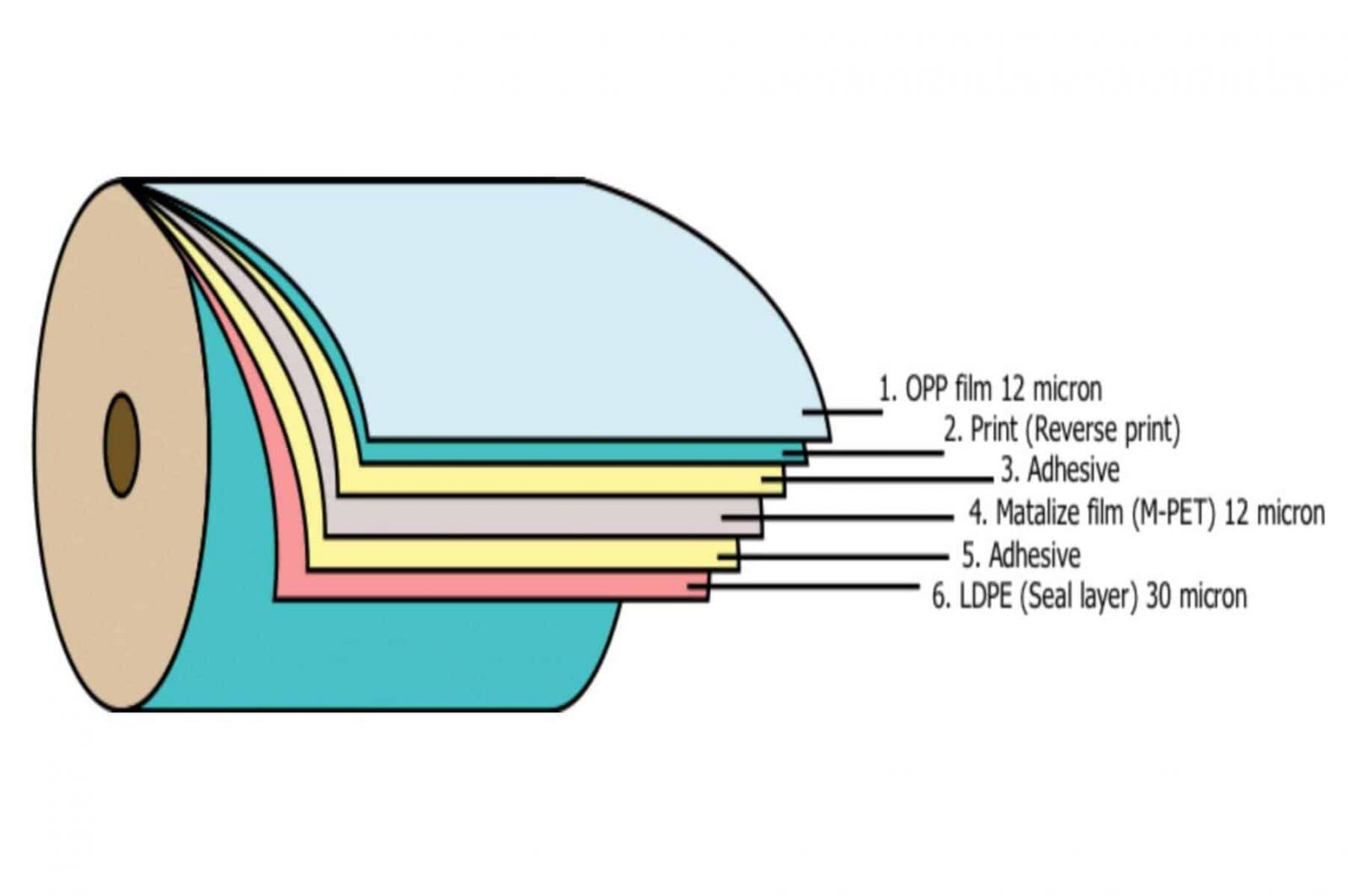
c. There is no difference in the production process of vacuum bags
In the production process of laminated film vacuum bags with 2 or more layers, these layers of plastic films will be produced separately in rolls, then put into the laminating machine to be laminated and pressed together. This film joining is done using heat or using an adhesive (glue). It should be noted that these roll of plastic film components need to be in the form of sheets (single film) and not tubes (double film) as usual. Single plastic film roll is obtained by halving the nylon tube at the end of the blowing process, before being wound onto the core tube. For example, to produce a 50 cm of single PE roll, the 50 cm double film roll will be cut in half at the end of the production process. And instead of just getting a finished double film roll, we get 2 single rolls of the desired size.
The original purpose of producing laminated plastic film was to help protect the printed images or characters on the film. This coating of protection not only prevents the prints from being scratched or faded, but also helps to increase the surface gloss significantly, creating great visual effects. But it has also been discovered that gluing multiple materials together can create a new type of film of higher quality. And since then, lamination technology to produce laminated film has developed a lot. Most membranes with different materials can be assembled using this method.
As noted above, this film joining can be done using heat or using an adhesive.
In the thermal lamination process, each roll of film will be run through a thermal roller preheating system, before being rolled into the main heating roller one by one. Here, the rollers squeeze the films together as tightly as possible, combined with an external radiant heat source to bring the film to the right temperature. After the films are laminated, they are cooled and rewound into rolls to wait for further processing steps such as printing or bag forming.
However, there are some types of plastic films that cannot bond themselves together solely by heat. The thermal lamination process is only suitable for 2- or 3-layer films, with the component resins having the melting point is not too big of a difference. Laminated films with more layers or more complex composition will require an adhesive lamination process.
In this process, film layers 2, 3 (and subsequent layers if applicable) are individually coated with adhesive by rollers, then blown with hot air to dry before being pressed onto film 1 by the main heating shaft. The adhesive or adhesive coating allows the film layers to be bonded immediately when the film is heated and pressed by the heating shaft. The film can then be fed into the cutter to cut and heat seal the bottom and side of the bag.
The reason for the heat sealing of both sides is because this laminated film bag is made up of two separate sides. This stage is different from ordinary plastic bags produced from tubular nylon rolls, just cut and weld the bottom. The heat press lines on vacuum bags are usually 0.5 to 1cm thick to ensure strength. And because there are 3 such heat-pressing lines, this type of bag is also called a 3-side bag.
There are suspicions that the use of adhesives will cause the bags to lose their food safety. But in reality, this glue is between the layers of membranes. They have no direct contact with the product inside and even with the outside environment. And this type of packaging has been proven harmless, approved for use in food containers.
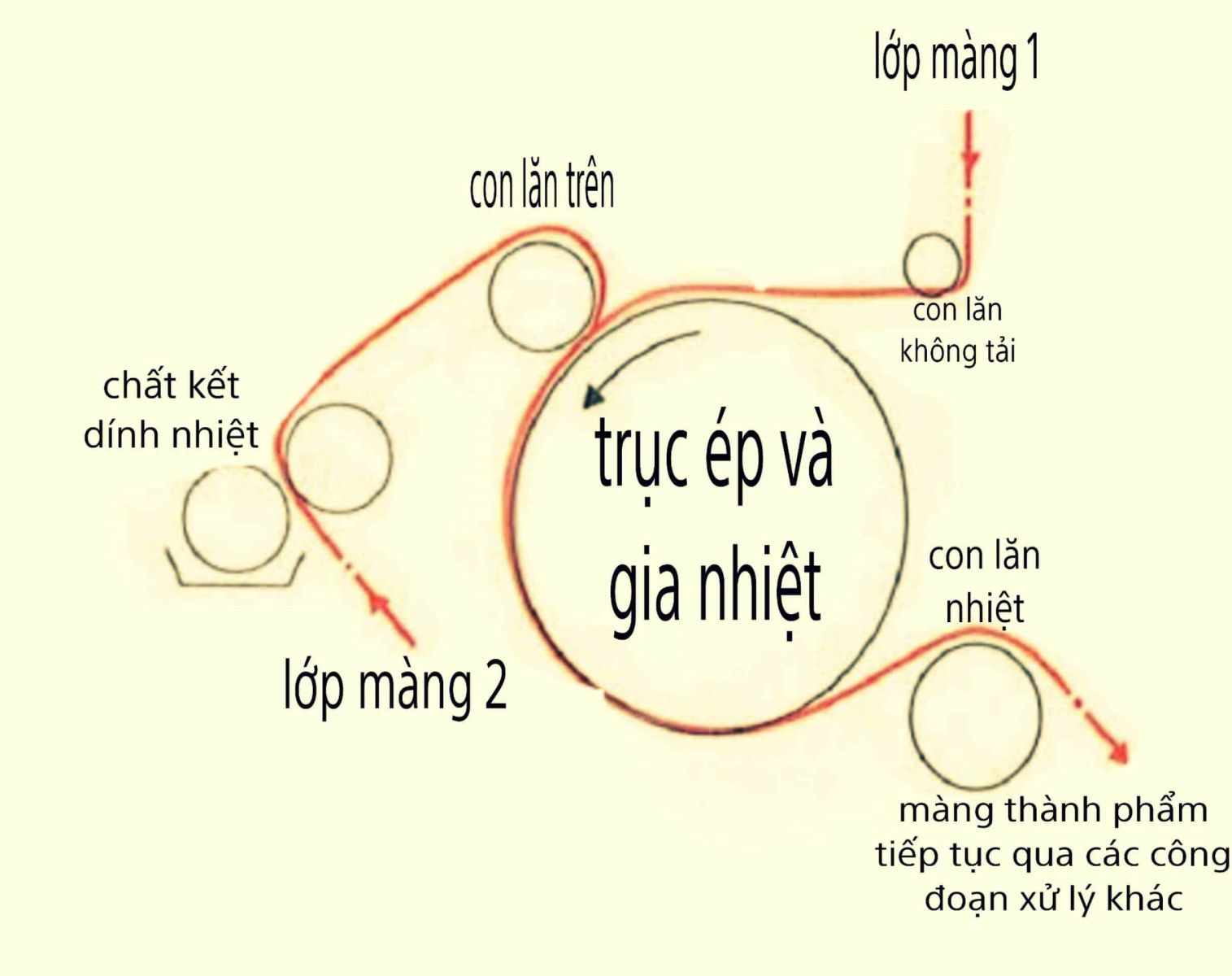
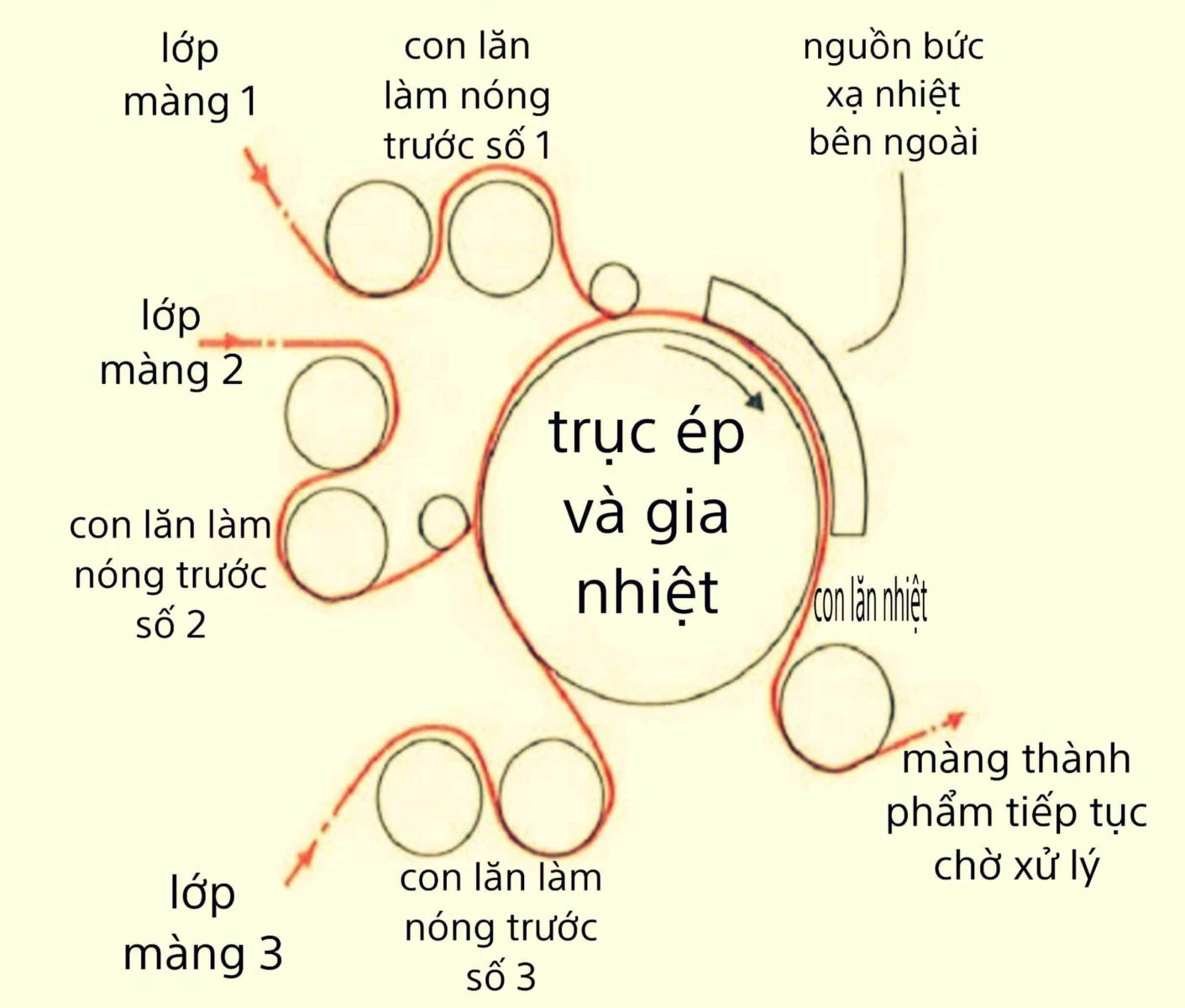
d. Vacuum PA / PE bags with outstanding packaging performance
Polyamide (PA) or Nylon is an engineering plastic obtained from the polymerization of amides and organic acids, which has a stable and malleable form at both very high and very low temperatures (from -60°C to 150°C). They are so durable that, with special reinforcement and treatment, they can replace metal. PA plastic film prevents fats, the penetration of oxygen, nitrogen, carbon dioxide and various odor particles very well. They are also highly transparent enough to clearly see the product behind the film. However, PA plastic has very poor moisture resistance and sealing performance.
Plastic films made from polyamides are still heat-sealable but require very high and precise temperatures, because PA resin has the characteristic of a particularly narrow soft temperature range. Unlike other thermoplastics that have a gradual hardening or softening process, PA cures rapidly at temperatures just slightly below the melting point. This makes it very difficult for packaging facilities to heat seal PA films, which often harden before they can be bonded together.
But when we add a layer of PE film to the PA film before pressing the sides and bottom to become a bag, we have a packaging product with excellent performance. Polyamide (PA) acts as a barrier to oxygen and odor particles, resisting heat and impact to form an impenetrable outer layer. Polyethylene (PE) is an FDA-approved direct food contact layer that prevents steam and helps heat-seal bags easily.
PA / PE bags with high performance and somewhat cheaper cost than other types of laminated packaging quickly become the typical and most consumed packaging in the frozen food packaging industry, especially those in the frozen food packaging industry. Export items have relatively long transit times.
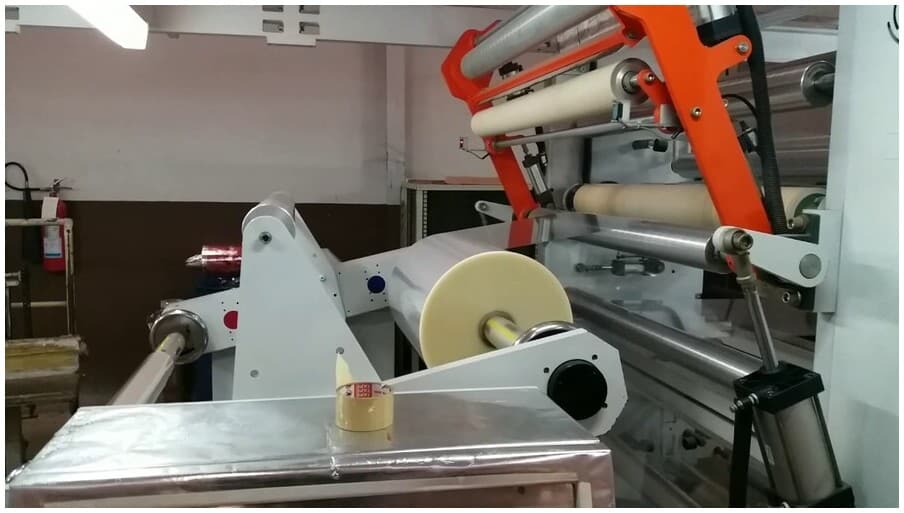
2. Notes when choosing to buy vacuum bags
During the epidemic period and international transportation was delayed, the demand for vacuum bags spiked to serve the transportation and storage of food for a long time, created a local craze with this type of packaging. Many businesses, establishments, and even business households have invested or improved machines to produce this type of packaging. It can be said that the current supply of vacuum bags is not lacking. However, because the packaging fever, the production of vacuum bags became rampant, the quality was unstable and the price was quite expensive, even counterfeit goods appeared. For people who are not familiar with plastic packaging production processes, it is difficult to distinguish between single-layer packaging and laminated packaging. It is extremely difficult to determine the material composition in a laminated packaging bag. Buying the wrong packaging can lead to the risk of leaking bags damaging the food contained.
To avoid buying low-quality and counterfeit goods, you should buy them at factories that directly manufacture this product line and ask to see the production process, or cooperate with reputable long-standing units in the industry.
With a small demand, you can consider buying grocery bags with common specifications on the market, sold through agents or packaging stores. The most common type of PA/PE vacuum bag is usually available in 10 zem or 12 zem thicknesses in sizes: 8 x 11, 10 x 15, 12 x 17, 13 x 18, 14 x 19, 15 x 20, 15 x 25, 17 x 27, 18 x 28, 20 x 25, 20 x 30, 20 x 40, 25 x 30, 25 x 35, 25 x 40, 25 x 45, 25 x 50 , 30 x 40, 30 x 45, 30 x 50, 35 x 50, measuring unit is cm.
Laminated film sealing bags are always heat-pressed on both sides and bottom (three-side pressing) which is also a point that customers need to pay attention to, to avoid confusion with thick 1-layer bags that only have 1 pressing line at the bottom of the bag.
Although it is a new product line and not a strength, but our Khang Loi company has also been providing vacuum PA / PE bags for many large seafood processing enterprises in Ho Chi Minh City. Chi Minh. This proves that our products are also of high quality, thanks to the investment in production on modern production lines, plus the available experience in the field of production of rolls and nylon films accumulated from before. Competitive price and large production capacity are also considered advantages for customers to choose PA / PE vacuum bags of Khang Loi Packaging company.